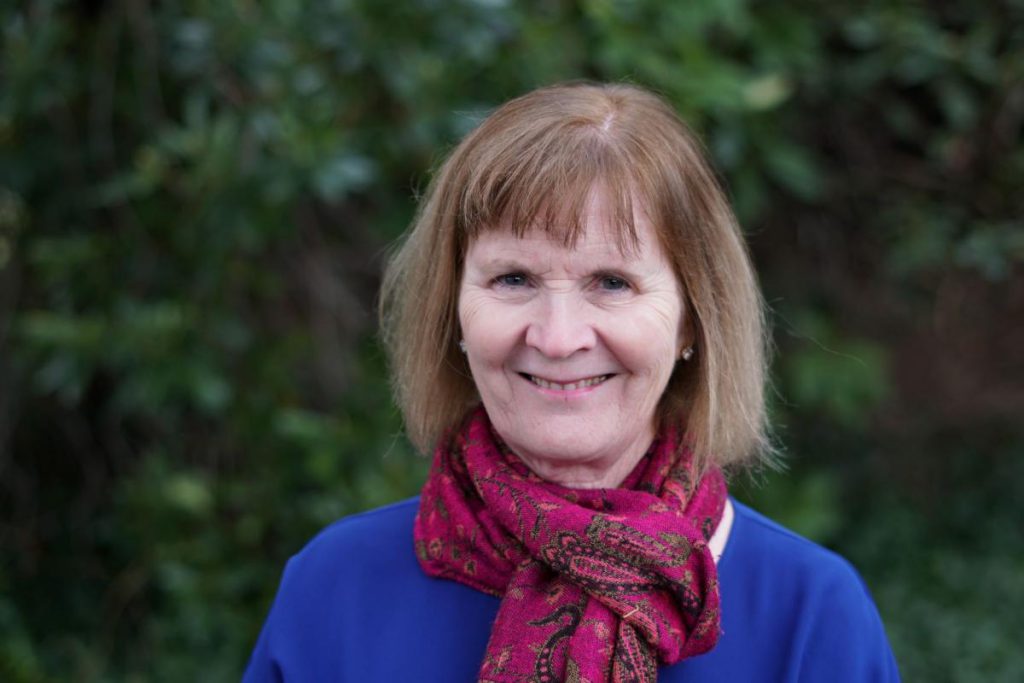
By Gary Forger, Special Projects Editor
This month we spoke with Barbara Ivanov, director of the Urban Freight Lab at the University of Washington. She is also chief operating officer of the school’s Supply Chain Transportation and Logistics Center. Previously, Ivanov worked on freight research projects with the U.S. Department of Transportation, the Strategic Highway Research Program and the National Academy of Sciences Transportation Research Board. Her focus included development of freight performance metrics, advanced freight data collection and analytic tools as well as freight-related economic impact analyses.
NextGen Supply Chain: The Urban Freight Lab’s primary focus is optimization of the final 50 feet of the urban goods delivery system. How are you doing that and who exactly is involved?
Ivanov: The Lab is a research partnership between its private sector members and the City of Seattle Department of Transportation. Urban Freight Lab members include retailers, urban freight carriers and tech companies in this space. Building developers and operators, managers and architects are also engaged in the Lab’s research.
We bring together both the public and private sector to solve problems in the final 50 feet of the goods delivery system that neither sector can solve alone. The members define the problems that the Lab works on.
NextGen Supply Chain: Plenty of people are focused these days on the final or last mile. But you’ve got it down to 50 feet. What’s your thinking here?
Ivanov: The final 50 feet is a concept that tracks the supply chain segment starting when delivery trucks stop at the curb, in an alley or in a loading bay underneath an urban tower. We’ve heard from our members that up to 60% of the time it takes to move goods from a distribution center to the final destination is spent in these final 50 feet.
Our approach is to analyze the process flow from the time the truck parks through loading of delivery carts, building entry going through security, to going door-to-door throughout the building to complete the delivery. What happens during this process has implications far beyond that single delivery.
Eliminating or decreasing failed first delivery attempts is the sweet spot for companies making deliveries. Our members say that 10 to 15% of all attempted deliveries to urban buildings are not completed. The right person may not be available to sign or the address is just wrong. That means the goods have to be returned to the distribution center and a second attempt made to complete the delivery. Those second attempts mean more trucks on the road, in the city and at the curb. The Lab can help change that.
NextGen Supply Chain: Tell us about the big picture here.
Ivanov: The City and Urban Freight Lab members also want to reduce truck dwell time in load/unload spaces. You can only do that by working with building managers and developers as their policies control how long it takes to complete deliveries in their building. Reducing dwell time makes each load/unload space more productive, you get more truck parking capacity without building more spaces. It can cut back the numbers of trucks circling the block looking for parking and so lower city traffic congestion.
Fortunately, there’s tremendous opportunity. We’re focused on a structured analysis of the final 50 feet in downtown Seattle by bringing together the City and supply chain companies. I’ll be talking about this at next month’s Modex show in Atlanta.
NextGen Supply Chain: What are you working on these days?
Ivanov: This month and next we’re pilot testing a common-carrier smart locker system located near loading bays under a 62-floor office tower. Now we already know that smart lockers work in general. We’re not pilot testing that. Instead, we’re trying to determine if smart lockers can reduce truck dwell time as well as reduce the level of failed first delivery attempts This is a test. But it’s a very focused test.
NextGen Supply Chain: On the surface, that sounds like it will change the final 50 feet in several ways.
Ivanov: If it works, it will.
Our data shows that nearly 80% of the time a delivery person is in this building is spent getting through security (12%) and riding elevators to different floors and going door-to-door to tenants (67%). The lockers, placed as close as possible to loading bays, could virtually eliminate that.
Deliveries would simply be put in lockers and recipients notified that their goods are waiting for them. They can then collect the goods when it is convenient for them.
We’re going to collect data for a couple of weeks and then analyze it. We will also have to make a judgment if smart lockers make business sense for the delivery companies. And just as important, will people in the tower adopt the use of common-carrier smart lockers.
NextGen Supply Chain: Once you come to your conclusions, what happens next?
Ivanov: We will then present our results to Seattle’s Department of Transportation. In fact, smart lockers are only a small part of the City’s effort to write a strategy for goods trip reduction.
The ultimate end game is public policy development that benefits all.
NextGen Supply Chain: That all sounds very exciting and forward looking. What’s next up for the Lab?
Ivanov: This year and next we’ll be doing pilot tests on the flexible use of curb space by delivery vehicles. That will be a big undertaking. And after that, we plan to take a look at smart lockers at commuter rail stations. We’ve got our work cut out for us for the foreseeable future.