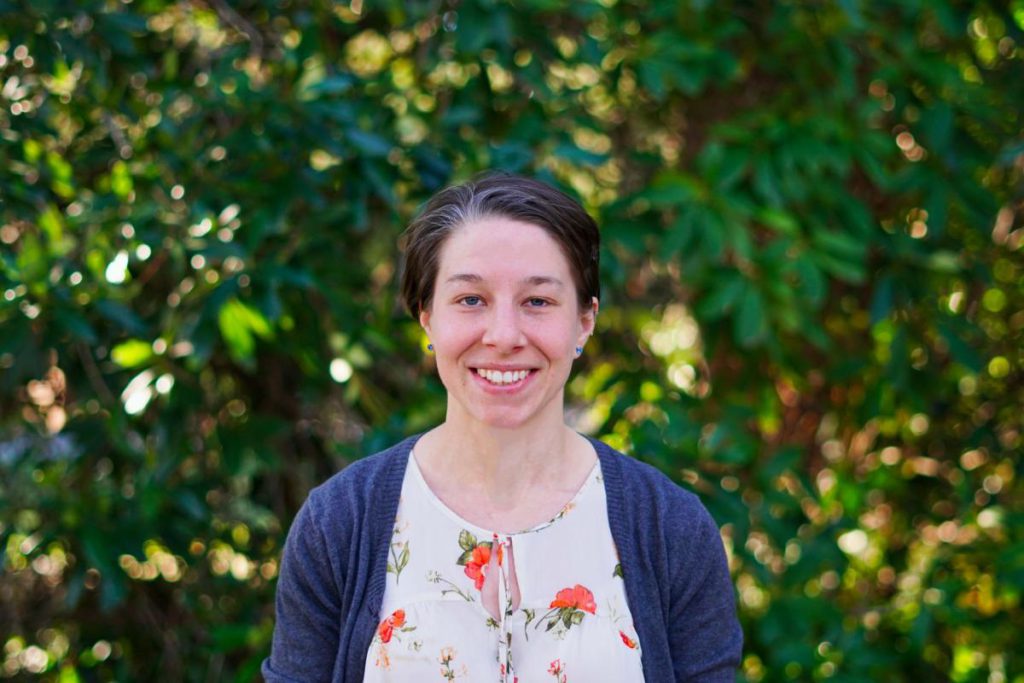
The Xinova innovator team is brainstorming and testing truly innovative solutions to improve the timeliness, quality and visibility of data for the malaria supply chain in Northern Nigeria. Joining our team is PhD Student, Chelsea Greene.
Chelsea Greene’s passion lies in developing optimization models to support a coordinated effort in building sustainable and resilient critical infrastructure, supply chain and logistics systems. She has experience developing optimization models and other decision support tools for applications in supply chain and logistics, personnel deployments, infrastructure resilience planning, behavioral incentive development for a wide-variety of stakeholders, and financial transparency. These tools have been applied to reduce lead-times for routing of lab specimens for the University of Washington Department of Laboratory Medicine, track supply and demand of life sustaining commodities for the Federal Emergency Management Agency (FEMA) following Hurricane Irma and Maria, and to improve financial transparency to donors for Zion Care Orphanage in Tanzania.
She is currently a PhD student in Industrial & Systems Engineering with a focus in Operations Research, and a Research Assistant in the Supply Chain Transportation and Logistics Lab at the University of Washington. She holds a MS in Industrial & Systems Engineering with a concentration in Operations Research and a BS in Accounting from the University at Buffalo, SUNY.
I believe this [project] will enable me to better develop innovative optimization models that are approachable and usable for decision makers in the national malaria programmes.
– Chelsea Greene
Volunteer at Zion Care Orphanage, Arusha Tanzania
Chelsea’s experience providing innovative solutions in low-resource settings, such as a Tanzanian orphanage, taught her four key principles to uphold in such challenging environments:
1. Start with small and simple solutions
2. Ask the people working daily in these settings what they need
3. Get others involved in the solution, especially the people who will be managing the product
4. Believe in yourself and the people you are working with
“I first realized the importance of keeping these factors in mind in 2014, when I traveled to Arusha Tanzania to volunteer at Zion Care Orphanage, which was the first time I really worked to implement a solution in a low-resource setting. I had just completed my Masters in Industrial & Systems Engineering, and I was ready to implement some fancy optimization models to improve all of the Orphanage’s problems. Then, I took my first bucket shower, and watched one of the orphanage managers trying to type a dollar sign on the computer, and being unable to due to a broken keyboard. This helped me realize maybe I should start smaller and simpler.”
She learned an invaluable lesson: to create a valuable solution, one must first understand the problem in its actual context. There was only one way to do that in the Tanzanian orphanage: talk to people.
“I sat down with the orphanage director to ask him. He mentioned a few things, a new English class curriculum, garden planting, and a way to highlight what is going on in the orphanage to donors. Then, in a discussion with orphanage manager he mentioned that he eventually would like to get into IT work. That is when the small but scalable solution came to me, I was going to work with the orphanage managers to teach them excel and give them exercises to build up an IT system themselves that provides information to donors. I figured that even if I failed at helping them build an information system, at least I taught the orphanage managers some excel skills.”
Her hands-off approach was sometimes difficult for her to stick to. Chelsea knew she could have built something quicker and spent more time ‘perfecting’ the solution. But she also knew that in the end it would be more beneficial if they accomplished the task themselves.
“Luckily, in this case it all worked out, and two years after its implementation, I got a message from one of the managers saying that he ended up upgrading the system in Microsoft Access himself!”
To say it was an inspiring two weeks in Tanzania for Chelsea would be “an absolute understatement.” On her last day, the director told her “you gave us more than money, you gave us knowledge, you came in here and made this Orphanage a better place than it was before.” He then asked her to give one last motivational speech to the kids.
“At the end of the speech I cheered YES WE CAN and NDIO NUEZA (yes we can in Tanzanian Swahili), and I meant it with all of my heart, because in those two weeks I learned how much of a difference I can really make. I believe we can all make a difference, we just need to believe in ourselves and have faith that we can do it. Since then, I have kept a picture of all of the kids cheering and hugging me on the background of my computer to remind myself of that moment, and all of the things I learned from this experience.”
African lessons in the North American context
Her experience in Tanzania fundamentally shaped her approach to understanding the complexity of problems even in Seattle. While working with the University of Washington Department of Laboratory Medicine to develop an optimization tool to improve their courier routes, she requested to go on ride alongs before conducting an analysis. In doing so, Chelsea learned vital details about the intricacies of cold chain supply chains, including the equipment required and the delicate nature of the different types of specimens.
“I heard stories from the couriers about how if they arrive 10 minutes after rush hour starts in certain areas, it can mean an extra 1 hour in the car.”
After interviewing management and performing her ride alongs, Chelsea was able to scope down the optimization model to two objectives: 1) Minimize lead times (from the time specimens are ready for pick-up to the time they are delivered to the lab for testing). 2) Reduce costs.
“Since optimizing against these two objectives will give different routing solutions, I wanted to make sure the tool was able to illustrate the tradeoffs between the two objectives (pareto optimality), and enable decision makers to adjust model priorities as necessary.”
Supply chain tools in hurricane disaster zones
While working as an Operations Research analyst at the Federal Emergency Management Agency (FEMA), Chelsea was requested to develop a tool to track supply and demand of life-sustaining commodities to the US Virgin Islands and Puerto Rico in the aftermath of Hurricane Irma and Maria. She had hands-on experience working at a warehouse, and synthesizing information for FEMA leadership. The goal was to synthesize information from FEMA’s National Resource Coordination Center (NRCC) where procurement decisions were made, and transportation logistics were set up, so that people on the ground had the information they needed to execute the last mile deliveries.
The NRCC had been activated for 60 days already. Chelsea spent an exhausting string of 12-hour days familiarizing herself with the problem by listening and asking rudimentary questions.
“What I realized is that despite feeling insecure to admit that I don’t know certain facts, on the coordination calls I got a feeling that there was a lot of lack of knowledge. I wanted to develop a tool that empowered the procurement, logistics, and last-mile team to incorporate systems think into their decisions. I also wanted the tool to clarify when there were gaps in information to provide complete transparency to what was not known to the people on the ground. Following the conclusion of the response phase, the tool was further developed so it could be used anytime the NRCC is activated.”
Fighting malaria in Nigeria
“Since starting my PhD program, I have been searching for a way to get involved in projects in this application area, because it is something to which I am very passionate about contributing my skillset. I believe this will enable me to better develop innovative optimization models that are approachable and usable for decision makers in the national malaria programmes.”