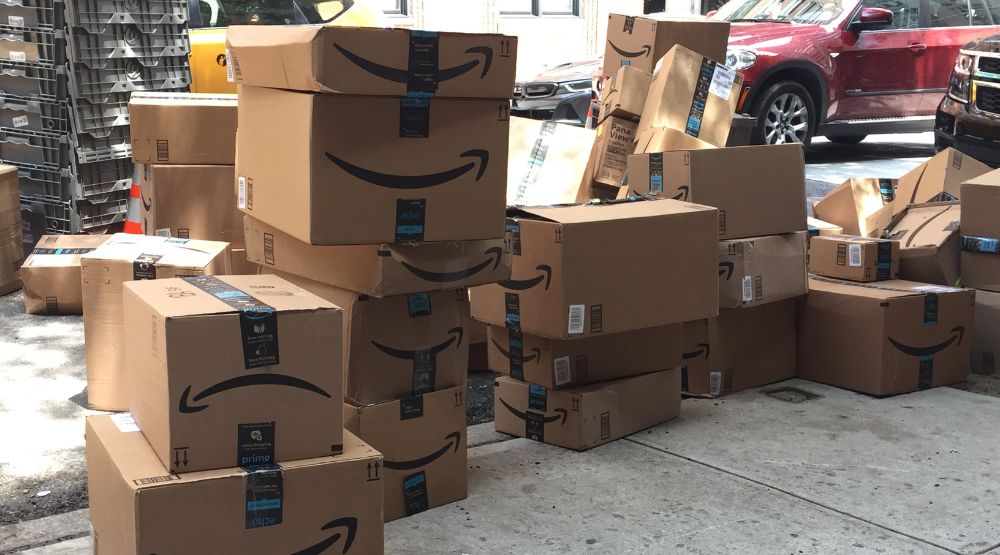
By Andrea Lillo
Every day in New York City, more than 2.3 million packages are delivered – left on doorsteps, piled up in lobbies, signed for by doormen. And the logistical challenges and environmental impact of those deliveries continues to grow – along with the number of packages.
Delivering goods across the U.S. continues to be a headache — and New York City’s aging infrastructure, massive congestion and island geography make it a unique challenge for supply chain logistics. How the delivery journey can be more efficient and sustainable —down to the last 50 feet —was the subject of a recent panel at the New York Chapter of the American Institute of Architects (AIANY), “Delivering the Goods: NYC Urban Freight in the Age of E-Commerce.”
“New York City is a consumer center. We demand a lot more goods than we generate or ship out – and it creates an imbalance,” said panelist Diniece Mendes, director of freight mobility, NYC Department of Transportation. The city needs to transform to meet the needs of tomorrow, with a unique multi-pronged approach, as delivery issues touch a lot of areas, she said. “It’s not a one-size-fits-all.”
“Sit on the approach to the George Washington Bridge any morning and you will see the magnitude of our trucking problem,” said Jack Schmidt, director of transportation engineering and program administration, NYC Department of City Planning. “There is just a line of trucks that stretches back into New Jersey.” Freight carriers are losing $5 billion dollars a year to congestion alone, said John Schettino, a mobility designer who worked on the soon-to-be-released AIANY report on delivery logistics in New York City, “Delivering the Goods.”
‘We’re a very built-up city’
One of the issues is the city’s lack of space – and the choicest areas are not generally used for freight. In cities where the price of real estate is high, spaces “disproportionally go to what we used to call highest and best use – housing,” said panelist Paul Lipson, principal, Barretto Bay Strategies. Therefore, the city compromised on locations for rail or maritime freight, leaving one option — trucking. “Because we’ve given away our working waterfront and we built over our rail yards, we conceded those spaces to high-value development” instead of freight, he said.
Due to zoning laws, the locations of many of these industrial spaces are generally lower-cost properties, which are usually near or adjacent to lower-income or disadvantaged communities, and impacts their lives, said Schmidt. In such a built-up city, there is a need to balance industrial zones with housing needs, he added.
The situation calls for more innovative thinking. “We need more local industrial space,” and not just for manufacturing, said Mendes. Like other cities, workers are not returning to offices in Midtown like they did before the pandemic, for example, and she said she wished politicians would talk about the possible opportunities for micro DCs or fulfillment centers in that part of the city.
Some places in Europe have used underutilized spaces as micro hubs, Mendes added — trucks may come to underused parking lots, for example, where packages can then be transported to cargo bikes for delivery. “Nothing sexy and exciting, but if there’s an empty space they can use, they will do that” – and perhaps in New York, that could include such spaces as underneath the 7 train in Queens.
“Part of the problem is someone gets tasked with ‘go find us a piece of land where we can build a building,’ and someone [else] gets tasked with ‘build us a building that works for trucks and distribution,’” said Schmidt. “No one is looking holistically.”
In addition, architects don’t normally design these industrial buildings, and that can also be an opportunity, said moderator Margaret Newman, practice leader Urban Places + Smart Mobility, Stantec. Freight facilities also don’t have to be large, single-story buildings, added Sandra Rothbard, founder, Freight Matters. “You can build up instead of out.”
Mendes wondered if the distribution journey can integrate more sustainable logistics and flow, similar to what LEED certifications are for other buildings. In Seattle, a pilot program used a common carrier locker system, which could be used by any delivery company (FedEx, UPS, Amazon) and cut down on the time delivery drivers spent in the building by 60%, as they could deliver the packages to one location, rather than going floor to floor to deliver packages.
New York City is ripe for solutions
AIANY’s soon-to-be-released “Delivering the Goods” study will be an interactive PDF comprised of about 70 pages of research, design strategies and detailed graphics. Those design strategies will include creating micro distribution centers that are more in step with the look of the neighborhood, expanding bike lanes and water freight and dedicating loading zones outside of buildings.
Already the city has incentivized cargo bikes, allowing operators to unload at curbs without having to pay the meter, Mendes said. It also has an off-hours deliveries program that aims to reduce congestion during the most critical times of the day. But that may not work for every business, as there may be issues with union-operated loading docks or when buildings can receive deliveries.
Already several large companies have tweaked their delivery strategies in the new normal, such as starting delivery earlier, so their trucks are back before the morning rush hour to reduce time in traffic, said Lipson. One cement company allows trucks to fill up after hours using a swipe card, he added.
Lipson also brought up an example that shows how some companies are getting ready for New York City’s congestion pricing plan (for which drivers looking to go south of 60th Street in Manhattan would be charged between $9-23 per trip; the program has seen many vocal opponents and proponents). A large beer distributor is looking into freight ferry to transport its beer from Hunts Point in the Bronx to Pier 17 in Manhattan, and then delivering product by hand cart, cargo bike or pallet jack within a quarter mile of the seaport district, he said.
“These are small, and they’re going to require a lot more policy making and a lot more land use thinking about how we leverage the waterfront,” Lipson said, and compromises will have to be made.
But New York is a good place to start. “New York is not unique, except for potential solutions,” said Mendes.
Getting consumers to reduce their freight footprint
While we know ordering online adds to the problem — no one’s giving that convenience up. “The impacts of this are so enormous on this very complex ecosystem that we’re all a part of that. To say people should order less stuff is ridiculous — people aren’t going to order less stuff unless there’s a price for ordering [more] stuff,” said Newman.
In general consumers don’t know the actual impact of their purchasing decisions, and panelists felt there should be more accountability — and cost —for shipping.
If someone is buying five items online and returning three, for example, there should be a charge for that, said Lipson. Otherwise, “we’re encouraging bad behavior.” Or, consumers could be charged more for getting items faster, so there’s a consequence, added Newman. Consumers could also be incentivized to walk short distances to pick up packages.
“Freight is public transportation —it’s all of our stuff that we buy and throw out,” said Rothbard. “We don’t treat it that way” because we think it doesn’t have anything to do with us, but everything is connected.
It’s “the high cost of free shipping,” she added.